A Few Words About Zinc Electroplating
You know that satisfying gleam of a perfectly zinc-plated surface? If you've spent any time in manufacturing, you've seen it countless times.
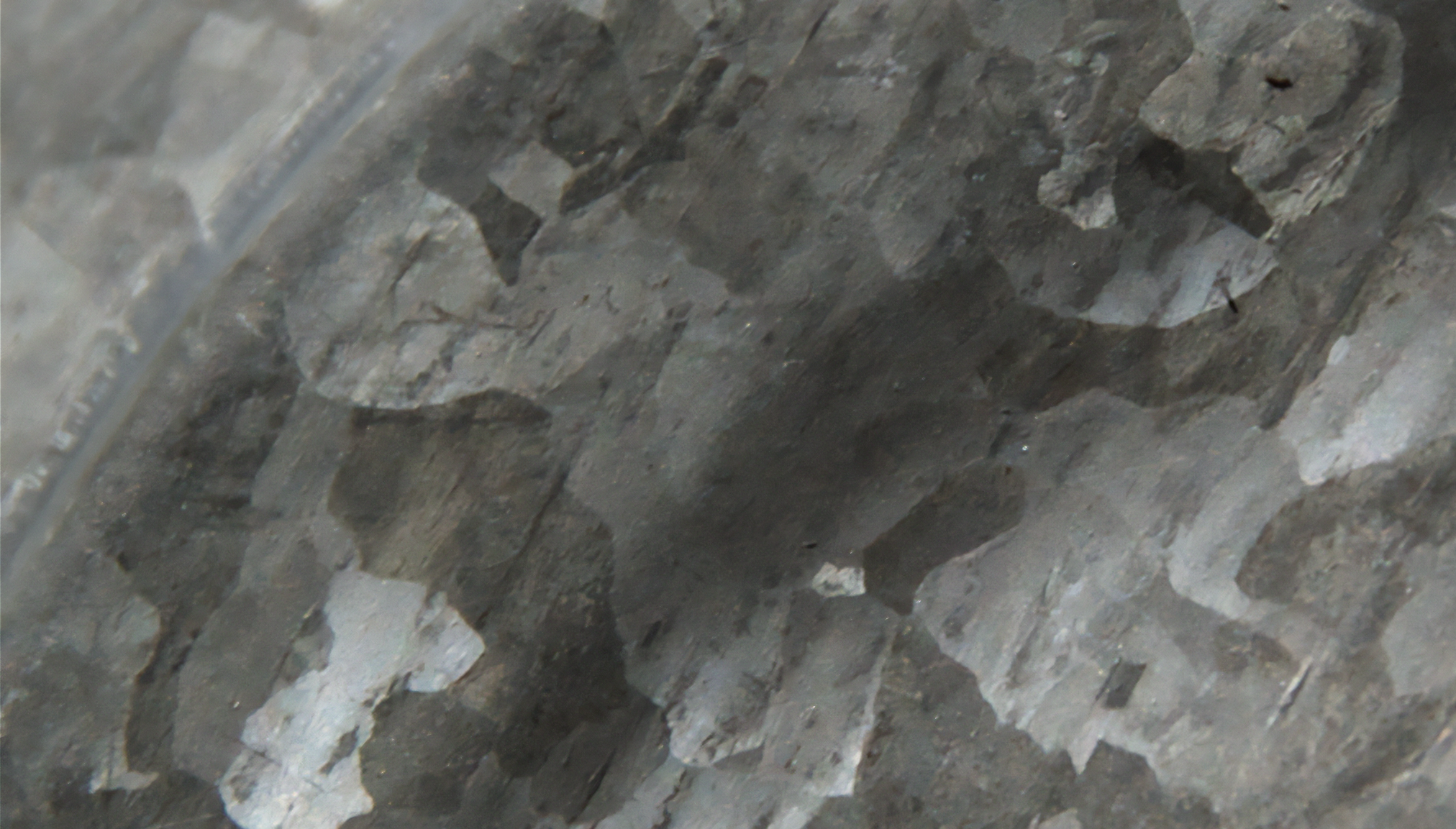
Zinc plating is one of the most reliable and cost-effective surface finishing methods we’ve got in our industrial toolbox.
Why Zinc? Because Protection Comes First
Steel and iron need armor, and zinc provides it, plain and simple. It sacrifices itself to shield the base metal—literally.
Here’s how: When exposed to the elements, zinc forms a tough barrier of zinc oxide and zinc carbonate. This layer blocks moisture and corrosive substances. And get this—even if the coating gets scratched, zinc still protects the exposed area, thanks to a nifty little trick called galvanic action.
Breaking Down the Process
Zinc electroplating might sound simple, but it’s all in the details. Let’s break it down:
Surface Prep:
Cleanliness is king. Grease? Rust? Even a speck of dirt can ruin everything. So, degreasing, acid cleaning, or even some elbow grease with mechanical scrubbing is the first step.The Plating Bath:
Here’s where the magic happens. The part takes a dive into a bath of zinc ions, and an electric current gets them moving. Slowly but surely, the ions coat the surface, building that protective layer.Post-Treatment:
After plating, most parts get a chromate conversion coating. Why? For extra corrosion resistance and, let’s face it, a little flair. You can go clear, yellow, olive drab, or even black—whatever fits the vibe.Challenges Along the Way:
- Hydrogen embrittlement can be a pain, especially for high-strength steels. A quick bake after plating usually does the trick.
- Uneven coating? That’s a geometry problem. Careful rack design and current tweaks can help even things out.
Quality Control Matters
How do you know it’s done right? Simple: Test it.
- Look at it: coverage and appearance matter.
- Measure it: X-ray fluorescence ensures the thickness is on point.
- Scratch it: adhesion tests don’t lie.
- And salt spray it: corrosion resistance is the ultimate benchmark.
Looking Ahead
The zinc plating industry keeps evolving. Environmental regulations are getting stricter, pushing us toward more sustainable practices. Many shops are moving away from hexavalent chromium post-treatments in favor of trivalent alternatives. They might be more expensive, but hey, protecting the environment is worth it, right?
Remember, successful zinc plating isn’t just about following procedures - it’s about understanding the why behind each step. When you get that part, you’re not just doing a job - you’re practicing an industrial art that’s been refined over decades.
Think about giving your plating line a thorough review. Are you getting the results you want? Could your process use some fine-tuning? Sometimes small adjustments can make a big difference in quality and efficiency.