Essential Guide to Electroplating
Learn about the electroplating process, key electrodes, and best practices in this in-depth guide for those seeking reliable metal finishing solutions..
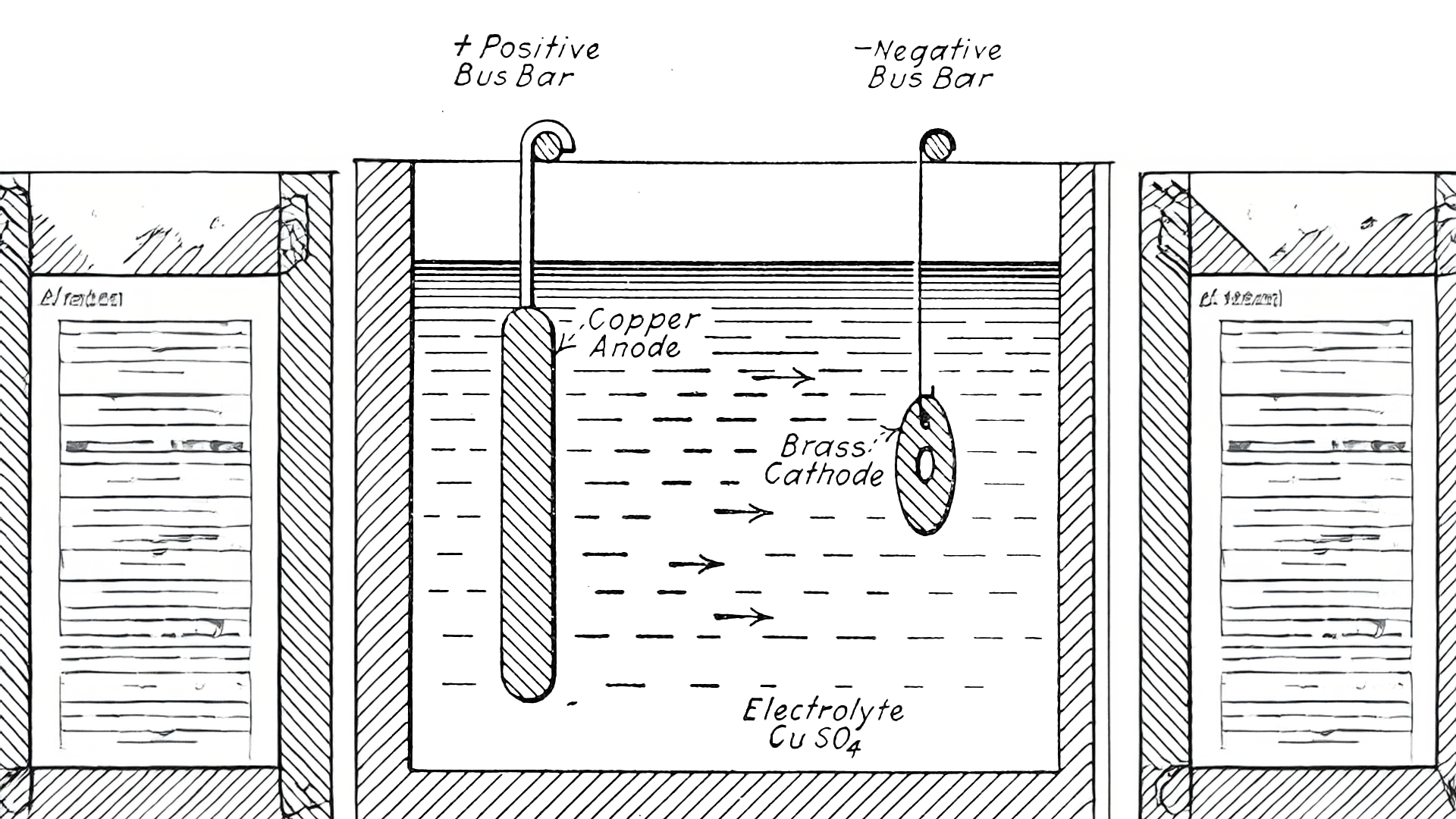
Introduction to Electroplating
Electroplating is a metal finishing technique used to deposit a thin layer of metal onto the surface of a workpiece. This process enhances the component’s properties such as corrosion resistance, wear resistance, and aesthetic appearance. For industrial engineers, understanding how electroplating works can help optimize product quality and extend component life.
In this article, we’ll examine the electroplating process step by step, the role of different electrodes, and the most common metals used in electroplating. Our focus is on clear, practical insights that ensure reliable and efficient outcomes.
The Electroplating Process
Overview of Electroplating
At its core, electroplating involves creating an electrical circuit in which a metal source (anode) dissolves into a solution (electrolyte) and then deposits onto the workpiece (cathode). The anode metal is selectively transported through the electrolyte, allowing for a controlled layer of metal on the cathode component.
Key Steps in the Electroplating Process
Surface Preparation:
- The component (cathode) is thoroughly cleaned to remove contaminants like oils, rust, or oxidation. Surface preparation methods typically include mechanical polishing, degreasing, and acid pickling.
- Proper cleaning is crucial for achieving uniform plating thickness and strong adhesion.
Immersion in Electrolyte Bath:
- After cleaning, the part is immersed in an electrolyte bath containing metal ions of the desired plating metal.
- This solution often includes additives to refine grain size, improve brightness, and control deposit properties.
Applying Electrical Current:
- A power supply introduces a direct current (DC) to the circuit.
- The workpiece (cathode) is connected to the negative terminal, while the anode is connected to the positive terminal.
- Metal ions from the anode or electrolyte solution migrate and deposit onto the workpiece surface.
Monitoring and Control:
- Key parameters, such as voltage, current density, temperature, and pH, are closely monitored. Adjusting these factors ensures consistent metal coating thickness and high-quality finishing.
Post-Plating Rinse and Finishing:
- The plated part is rinsed to remove residual chemicals.
- Additional finishing processes, such as polishing or passivation, may be applied to enhance surface properties.
(Source: “Modern Electroplating,” M. Schlesinger and M. Paunovic, John Wiley & Sons)
Main Electroplating & Electrodes
Anode and Cathode
Electroplating relies on two electrodes connected to a power source:
Anode (Positive Electrode):
- The anode typically consists of the plating metal itself (e.g., nickel, chromium, or copper).
- In some processes, an inert anode (e.g., platinum) is used, and metal ions are supplied by a metal salt in the electrolyte.
Cathode (Negative Electrode):
- The workpiece to be plated is connected to the negative terminal, attracting positively charged metal ions.
- Metal ions from the electrolyte deposit onto the cathode, forming the new metal coating.
For more on electrodes, see Electroplating Electrodes.
Common Metals Used in Electroplating
- Zinc:
- Primarily used for corrosion protection on steel components.
- A zinc coating acts as a sacrificial layer, protecting the underlying substrate from oxidation.
- Nickel:
- Offers excellent wear resistance and hardness, often used in industrial applications such as aircraft and automotive parts.
- Also adds an attractive luster when polished.
- Copper:
- Provides good electrical conductivity, making it ideal for electronic components and decorative finishes.
- Serves as an undercoat in multi-layer plating systems to improve adhesion.
- Chromium:
- Adds a hard, shiny surface with superior wear resistance.
- Commonly seen in decorative automotive trims and machine components requiring a protective surface.
Specialized Electroplating Techniques
- Electroless Plating
- Uses a chemical reduction process instead of an external power source.
- Allows for uniform coating on complex geometries, particularly beneficial for small holes and blind vias.
- Rack and Barrel Plating
- Rack Plating: Best suited for larger or more complex parts. Components are individually mounted on racks to ensure uniform exposure.
- Barrel Plating: Ideal for large volumes of small parts (e.g., fasteners, pins). Components tumble inside a barrel, providing cost-efficient finishing.
(Reference: ASM Handbook, Volume 5)
Best Practices for Industrial Engineers
Design Considerations
- Part Geometry:
- Avoid deep recesses and sharp corners if possible. These areas may lead to uneven plating thickness.
- Incorporate drainage holes where needed to prevent solution entrapment.
- Coating Thickness Requirements:
- Define the appropriate thickness to balance cost and performance.
- Over-plating can lead to material waste and dimensional changes, while under-plating offers insufficient protection.
- Substrate Compatibility:
- Different substrates have unique plating challenges. Select electrolyte chemistries that align with the base material.
Quality Control and Maintenance
- Routine Bath Analysis:
- Monitor concentrations of metal ions, pH, and additives to maintain consistent results.
- Implement a scheduled bath purification process to remove contaminants.
- Process Validation:
- Conduct periodic thickness and adhesion tests using non-destructive and destructive methods.
- Record process parameters to trace and rectify any production anomalies.
- Equipment Maintenance:
- Regularly inspect anodes, racks, and other plating equipment.
- Replace worn parts to minimize defects and downtime.
Conclusion
Electroplating is a critical process for industrial engineers looking to enhance metal surfaces for improved durability, corrosion resistance, and functionality. By understanding the science behind the electroplating process, carefully selecting electrodes and metals, and adhering to best practices, engineers can optimize their metal finishing projects for long-lasting and cost-effective performance.
Whether applying a protective zinc layer or adding a decorative chrome finish, proper control of the electroplating process ensures reliable outcomes and a competitive edge in demanding industrial environments.
References:
- M. Schlesinger and M. Paunovic, Modern Electroplating, John Wiley & Sons.
- ASM Handbook, Volume 5: Surface Engineering, ASM International.
(Note: For general reference on electroplating definitions, you may visit the Wikipedia Electroplating page.)